从原料到成品全程可控可追溯,为食品安全保驾护航
推进数字化转型升级,降本增效提质,助力食品行业高质量发展
行业面临的挑战
食品质量安全
-
食品安全法规的严苛以及《肉制品生产许可审查细则》的实施,生产从原料的源头到复杂的生产过程,如何确保食品的质量安全,是企业面临的首要挑战 。
-
配料工序。原料品种多,有些食品添加剂用量小,错配、漏配料会直接导致产品质量问题。
-
投料作业。如何避免投错料,是保证产品质量的关键作业。
消费者对食品质量与追溯提出了更高的要求
-
《食品安全法》对质量控制与追溯提出更为严格的要求。
-
纸质记录生产过程信息,各部门信息共享存在障碍,无法及时进行质量控制、改进和追溯。
-
当产品出现质量问题,不能及时、准确的找到原因。
无法实时获取制生产过程信息
-
生产进度不透明,计划执行有效性难以保证;
-
难以全面了解和控制生产所有环节信息;
-
生产过程的实际投入与产出 。
-
生产过程人工记录繁琐。
-
纸质传递BOM,配方保密性差。
生产成本核算难
-
批生产过程的物料、人员、设备的实际投入;
-
在制品的产出;
-
成品及副品的产出。
-
如何快速准确的核算成本。
解决方案
基于惠和批控制系统(batch Control Application),实现从原料到成品整个生产过程的控制与质量追溯,实现对生产批次的质量管控,有效防止人为因素在生产过程中的影响,确保产品质量的稳定性;关键工序生产控制过程自动记录人、机、料的投入,报工单记录成品/在制品的产出,提高成本核算的准确性;生产参数、过程工艺参数自动采集分析,建立完整的批生产记录,实现产品质量的有效追溯。
批控制系统。是运用精益生产、标准化管理、可视化管理等生产管控理论为依据,以软件技术、条码自动识别技术,结合手持终端(PDA)、工业智能终端设备(Terminal),实现于从原料到成品整个生产过程的控制与质量追溯,提高制造过程的数字化、精益化、透明化,提升产品质量、缩短生产周期、提高生产效率。控制的关键工序包括:原料>>配料>>投料>>生料加工 >>成型>>热加工>>包装>>成品。
-
原料层:实现批次管理、合格供应商管理、先进出控制、在制品管理;
-
配料层:配料防错(AWS)系统实现添加剂的称量控制,防止人为因素导致的错配、漏配;液体料实现自动输送与计量。
-
投料环节:实现投料品种、数量的控制,避免错投、漏投,确保产品质量,实现物料投入的准确核算。
-
生料加工:实现物料投入与产出的控制与核算;
配料称量控制
小料配料称量的准确与否,对产品的质量起至关重要的作用。在实际生产过程中由于人为因素造成的错配、漏配、称量精度低等现象严重影响的质量,配料称量控制系统可以有效的解决上述问题,确保产品质量的稳定性与可靠性,减少资源的浪费,降低生产成本。并可实时统计原料在某段时间内的实际消耗值与理论用量值。
特征:
1. 防止异物品。
2. 确保称量精度、称量准确和完整。
3. 实现配料记录的可追溯性。
4. 操作简单,减少双人复核,降低用工成本。
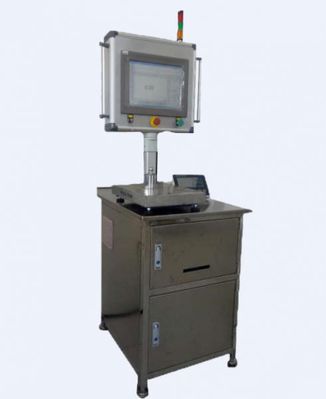
产品工艺管理。为产品建模定义如何生产,包括生产工序、工步、物料规范(BOM)、设备规范、人员规范、质量标准(产品指标)等。同时建立与生产实际相对应的数字化工厂模型,满足集团用户多工厂、多产线、多存储区域建模。
生产计划与调度。从ERP导入生产订单,系统依据工艺路线分解为工序作业计划,排产后下发到现场。对车间的生产情况进行实时监控,获取生产相关数据,跟踪生产进度(开始、完成状态),支持大屏幕监控。
物料与生产物流。仓储物流根据排产计划及进度,按时间段、工序生成物料配送计划,由仓库人员配送到指定位置;生产完成的在制品、成品入库,实现生产物料的管理、追踪。
质量管理。根据工艺需求进行检验控制,通过事件可以触发检验请求,由检验员执行检验,反馈检验结果,进行质量监控和追溯。
设备运维。设备运维通过车间设备管理模块统一维护,提醒和指导设备人员定期保养,记录维修保养结果。设备维保计划与工序作业计划需相互协调,以保证生产正常进行。确保设备安全、稳定、经济运行,实现设备资产价值最大化,为企业生产运营服务提供保障。
物联网关。采用本地化部署,根据工艺要求,设定生产参数,生产执行过程工艺参数自动采集分析(如:热加工设备的能耗采集),并实现与批次记录的关联。
收益
质量提升
实时准确的配料、投料控制,使得产品质量得以有效控制;
产品批次可追溯
使用的原料批次可追溯;作业人、作业时间可追溯;设备及过程工艺参数可追溯
生产车间数字化
工艺参数自动推送到设备,生产过程工艺参数自动采集分析,实现人机料法测的控制与融合。
生产成本核算及时准确
在生产控制过程自动记录物料、人员、设备的实际投入,提高制造成本统计实时准确。
生产管理提质增效
实时获取生产信息,提高生产计划透明度,全面了解和控制生产所有环节信息。
设备价值最大化
减少停机时间,为生产提供保障