利用AWS防错提高配料准确性
原料品种多,以前配料容易出错,对工人依赖性强,管理压力大,使用防错系统后,问题解决了。
---客户使用后的评价
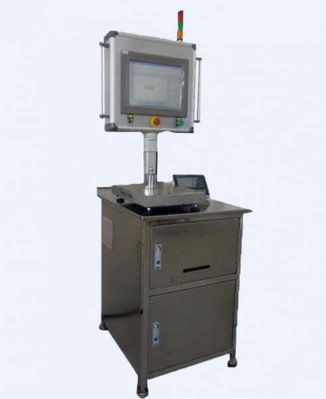
AWS防错系统
小料配料称量的准确与否,对产品的质量起至关重要的作用。在实际生产过程中由于人为因素造成的错配、漏配、称量精度低等现象严重影响的质量。配料称量控制系统可以有效的解决上述问题,保证产品质量的稳定性与可靠性,减少资源的浪费,降低生产成本。并可实时统计原料在某段时间内的实际消耗值与理论用量值。
特征:
1、防止异物品。
2、确保称量准确、完整。
3、确保称量精度。
4、实现配料记录的可追溯性。
5、杜绝人为因素。
6、操作简单,减少双人复核,降低用工成本。
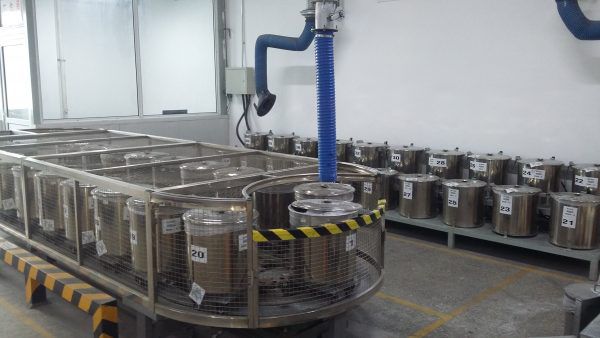
便于工人作业的自动给料转盘
1、首先在系统设定料桶与原料的一一对应关系。加料时,扫描原料条形码,对应的料桶自动旋转到加料位置,且只有此料桶可以开启,确保加料正确。
2、配料过程。根据当前配方所需原料,系统计算最短路径,自动将物料桶输送到称量位置,且只有此料桶可以开启,确保取料正确。称量在配方设置的公差内,按确定按钮,自动旋转到下个料桶。配料称量结束,按确定按钮,系统自动复位。
3、采用变频调整速、最短路径计算,自动输送,减少工人走动,提高配料准确度与效率。
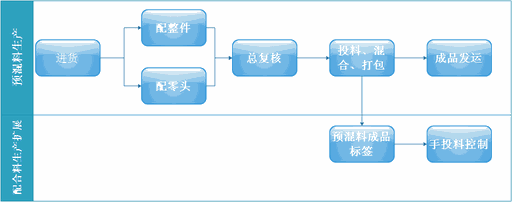
随需应变,解决更多生产问题
从原料源头抓起,对生产过程的原料、配料、投料、包装、发运等关键工序加以控制,防止人为因素的发生,确保产品质量的可靠性,由过去产后检测,改变为产前、产中控制和产后溯源,保证产品全程优质、安全、高效生产。
系统包括: 1、原料批次管理,可选的先进先出控制; 2、整件、零头的配料称量控制; 3、总复核与投料控制;4、打包控制; 5、成品发运 ……
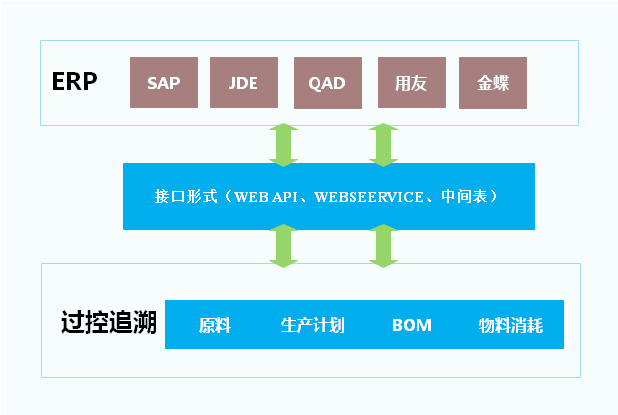
与ERP系统接口,业务运转更流畅
与现有ERP对接,生产计划、BOM可对从ERP直接导入,避免二次输入,减少出错,更好的提高效率。
任务作业结束,所有物料消耗返回ERP扣料,出库更精准。
系统支持以下ERP系统:SAP、JDE、QAD、金蝶、用友。
用户收益
提升质量
避免错配、漏配、称量不准等人为因素造成的影响,确保配料称量准确。
提高产品质量、减少原料浪费、提高公司效益。
节省用工
采用傻瓜式操作设计,经过简单培训即可按照操作提示作业,减少对熟练工人的依赖。
只需一个人就可精确完成配料称量作业。减少双人复核、降低用工成本、提高工作效率。
可追溯性
将原料批次管理、配料称量一体控制,建立产品质量追溯体系。
更好满足客户要求,有机会获取更多的订单。
客户评价
提升质量,减少浪费
”人工操作难免有差错,有时多了、少了,有一次防老剂忘加了,量很小,出厂没检出来,产品流到市场上没几个月,反映出现问题。公司不但有损失,关键影响声誉”
“现在使用称量系统,操作规范了,质量也提上了,以前的问题不用担心了。”
取消双人复核,节省用工
”我们的原料品种多,配料工文化水平低,有时会把相近的物料搞混了,公司为此增加双人复核,用工成本增加了。”
“使用称量系统,工人经过简单培训就可上岗,操作简单了,取消了双人复核,质量得到控制,成本也降低了。”
质量可追溯
“我们给主机厂做配套,客户要求很高,尽管实行16949管理,但人为因素还是比较多,客户验厂,总是提出这样、那样的问题,我们也担心出问题,不但索赔,还可能取消供应资质。“
”使用称量系统后,配料准确了,质量也好追溯,客户满意了,我们的订单也逐渐增加了“

提高管理水平
”我们在全国有几家工厂,出现质量问题,要去现场分析原因,制定措施,但有些人为因素还是没从根本解决。”
“现在全程控制,操作正确了才能往下走,现场管理提高了,质量可控了,我的压力也轻了许多。”
物料好盘点
”小料原料品种比较多,每天频繁的领料使用,到了月底盘点,理论量、领用量和生产量人工统计麻烦也不准确,造成财务不好核算成本。”
“使用称量系统,系统自动记录汇总理论与实际的领用量和使用量,盘点非常方便,也很准确,也节省了时间。”
满足客户高质量要求
”公司给丰田、本田、日产、马自达等汽车整车厂配套,客户对产品质量要求非常高,要求实现生产过程控制和质量追溯,但现在人工配料,手工记录,客户对这种方式不信任,达不到客户要求。”
“使用AWS系统后,配料没有再出过错,数据也是自动记录,客户来审核也非常满意。”
产品方案,按需配置
基础配置
单点工作站
- 基本配料操作,1个用户
- 配方管理、生产计划、物料统计
- 多种外设选配
- 即插即用,免安装,在线培训,免费电话支持
扩展配置
多工作站协同作业
- 采用企业级网络数据库,可以扩展多个称量点
- 配方分段协同作业
- 在办公室即可完成 计划任务的下达
- 支持工程师上门安装培训与在线培训
升级配置
多部门协同工作
- 升级成MES系统,实现全程控制
- 可升级的模块投料控制、成品发运
- 全程追溯
- 工程师上门安装培训
15年历程,助力600+用户精益生产,提质增效赢取新的业务增长。
合作伙伴
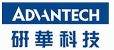
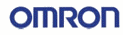
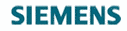

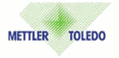